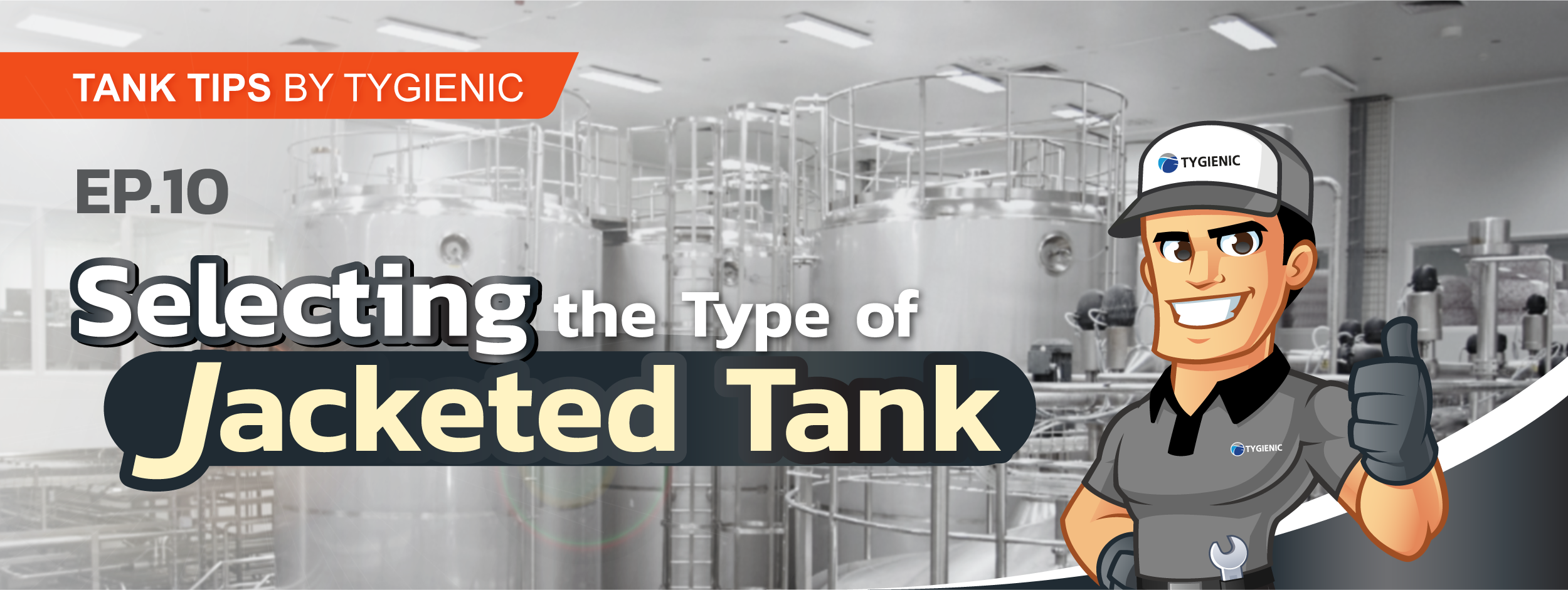
Selecting the Type of Jacketed Tank
What is a Jacketed Tank?
In industrial settings, tanks can be categorized based on their structure into three types:
1. Single Wall Tanks
2. Double Wall Tanks (Insulated Tanks)
3. Triple Wall Tanks (Insulated Tanks with Heating/Cooling Jackets)
SINGLE WALL (NON-INSULATED TANK)
DOUBLE WALL (INSULATED TANK)
TRIPLE WALL (INSULATED TANK WITH HEATING/COOLING JACKET)
A single-wall tank is suitable for products where temperature control is not required, such as general storage or mixing tanks used at room temperature. However, if there is a need to maintain the temperature of the product in the tank, such as keeping hot water hot or cold milk cold, the tank should be insulated to prevent heat/cold loss from the product to the environment. If we need to either increase or decrease the temperature of the product in the tank, or if there is a need to maintain the product's temperature for extended periods, a jacketed tank would be ideal.
Why Use a Jacketed Tank?
In various production processes, there are multiple steps where we need to adjust the product's temperature in the tank. One convenient method is to use a jacketed tank to introduce a heat exchange medium (such as steam, hot water, cold water, or glycol) to transfer heat through the tank walls into the product.
For some products, it is sometimes necessary to maintain the temperature for an extended period, such as raw milk that isn't used up within a day and needs to be stored overnight or for several days. If the tank is only insulated, it’s similar to storing milk in a thermos: the temperature doesn’t change much during the day but gradually rises overnight, affecting the milk's quality. Hence, designing a tank with an additional cooling jacket is akin to putting the milk in a refrigerator, thereby lowering its temperature.
Types of Jackets
Jacketed tanks come in various types, each suited to different applications and budgets. The most common types are:
1. Dimple Jacket
A dimple jacket consists of a metal sheet stamped with dimples. The dimpled sections are welded to the inner tank wall, while the undimpled sections create a space for the heat exchange medium to flow through. Dimple jackets are welded at frequent intervals, which reinforces the inner tank, making them lightweight and more cost-effective compared to other jacket types. However, the frequent welds reduce the space for the medium to flow, limiting the flow rate and making it less suitable for high-temperature differential heat exchange. Dimple jackets are ideal for maintaining temperature and are widely used due to their cost-effectiveness.
2. Half Pipe Jacket
A half pipe jacket is created by splitting a pipe in half and welding it to the inner tank wall, allowing the medium to flow through the pipe for heat exchange. This type of jacket adds some reinforcement to the inner tank and allows for a higher flow rate of the medium than dimple jackets, improving heat exchange efficiency. However, half pipe jackets are more expensive than dimple jackets.
3. Chamber Jacket
A chamber jacket involves placing another cylindrical tank over the inner tank and welding it closed at the top and bottom, creating a large space for the medium to flow through for heat exchange. The chamber jacket allows the medium to flow most freely, providing the highest heat exchange efficiency compared to dimple and half pipe jackets. However, this makes the tank heavier and more expensive. Chamber jackets are suitable for tanks requiring high-temperature differential heat exchange, such as boiling, heating up, or cooling products. The thickness of the inner tank can be reduced by adding flow direction barriers within the space between the inner tank and jacket, known as a Spiral Jacket.