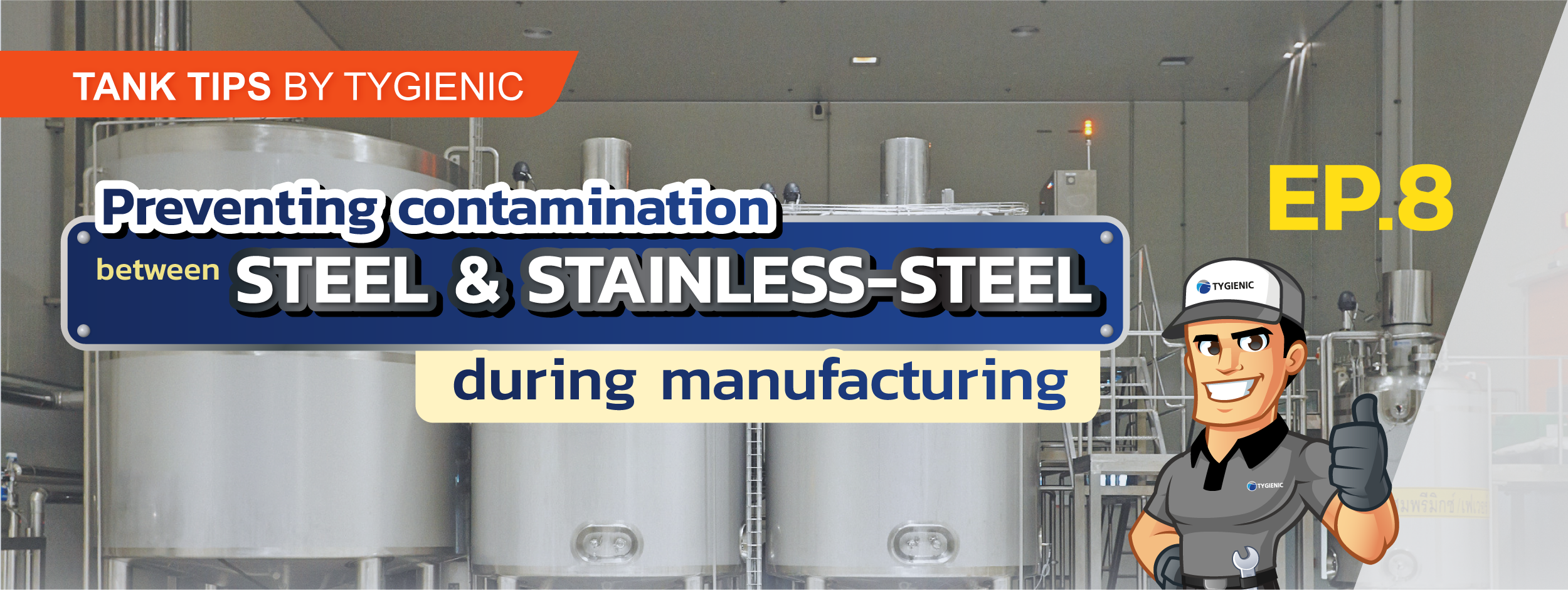
Preventing contamination between steel and stainless-steel during manufacturing
Preventing contamination between steel and stainless-steel during manufacturing is crucial. Contamination of stainless steel with rust during production can significantly reduce its lifespan, disrupt intended design functionalities, and potentially compromise the final product's integrity under heavy usage.
Rust formation on stainless steel stems from the compromise of its protective chromium oxide layer. For instance, scratches on stainless steel surfaces coupled with moisture can trigger a reaction with iron particles, leading to rust formation. Moreover, the presence of carbon steel particles adhering to the surface can expedite corrosion and compromise the protective oxide layer.
Several factors contribute to rust formation during manufacturing:
1. Contact between steel and stainless-steel components: Direct contact between stainless steel and carbon steel components can induce galvanic corrosion, hastening rust formation.
2. Direct contact with steel materials: Assembly of equipment using steel materials in direct contact with stainless steel components can foster corrosion.
3. Metallic dust from steel tank production: Metal dust generated during the production of steel tanks in nearby areas can settle on stainless steel surfaces, promoting rust formation.
4. Use of improper materials: Utilizing inappropriate materials such as abrasive stones or incorrect steel types can foster contamination and corrosion.
To mitigate rust formation during manufacturing, implementing preventive measures is essential:
- Isolation: Ensure the separation of steel and stainless-steel components throughout production to prevent direct contact and galvanic corrosion.
- Material selection: opt for materials compatible with stainless-steel and refrain from using abrasive materials that may scratch its surface.
- Cleaning procedures: Implement thorough cleaning protocols to eradicate any contaminants or metallic dust that may settle on stainless steel surfaces during production.
- Surface protection: Apply protective coatings or finishes to stainless-steel surfaces to augment corrosion resistance and uphold the integrity of the chromium oxide layer.
Addressing these factors and implementing appropriate preventive measures can effectively prevent contamination, thereby extending the lifespan of stainless-steel components and ensuring the quality and durability of the final products.
Furthermore, to prevent rust formation and preserve the chromium oxide film on stainless steel surfaces throughout the manufacturing process, it is essential to adhere to key practices:
1. Storage of Stainless Steel: Categorize and store stainless steel separately from steel in areas where they won't come into contact. Utilize materials like wood, plastic, or stainless steel for shelving.
2. Production Process: Refrain from using steel tools and equipment to reduce contact. If unavoidable, use alternative materials for protection, such as stainless-steel liners, lining, strong backs, roller supports, and others.
Using Teflon rollers for laying stainless steel
Using PVC for stainless steel surface protection
3. In the production process, consider separating factory areas for steel and stainless-steel production to prevent iron dust particles from causing rust issues on stainless steel surfaces. If separation isn't feasible, utilize adequate barriers or equipment to prevent iron dust contamination.
4. When utilizing consumable materials, ensure correct categorization. Utilize only abrasive stones suitable for stainless steel work to prevent contamination. Consequently, effective prevention of contamination between steel and stainless-steel during manufacturing will ensure that tanks produced with stainless steel have a lengthy service life per design specifications and remain free from rust contamination issues upon use.